Оглавление:
Введение
Планирование производства на любом современном предприятии — сложный, многоэтапный и крайне трудоемкий процесс. Производственный план, родившись в кабинете генерального директора в виде годовой программы выпуска, тщательно детализируется в недрах производственно-диспетчерского отдела, «размазывается» по компьютерам и флипчартам1 цеховых диспетчеров, оседает в папке мастера и, наконец, заканчивает свой путь в невзрачном промасленном сменно-суточном задании (рис. 1). И уже на следующий день вновь возрождается, словно птица Феникс, в отчетах и рапортах на «планерках» и совещаниях.
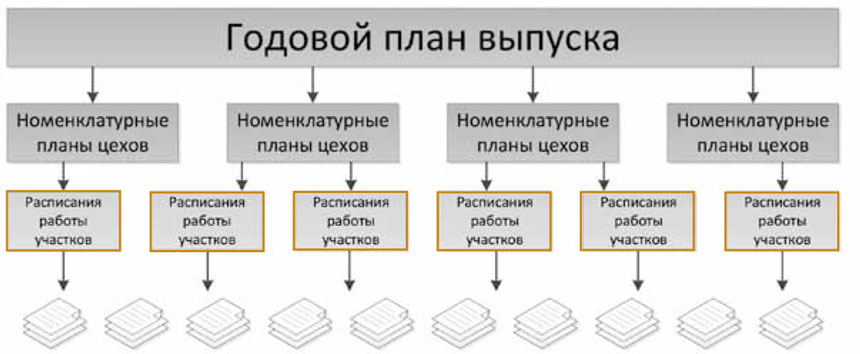
Рис. 1. Схема производственного планирования
При этом в эпоху стремительного изменения конъюнктуры рынка, высокой конкуренции и индивидуализации спроса к гибкости и оперативности производственного планирования и перепланирования на каждом из этих этапов предъявляются высочайшие требования, эффективное выполнение которых возможно исключительно с применением соответствующих информационных и управляющих систем [1].
Рассмотрим ключевые задачи производственного планирования, их взаимосвязь с другими бизнес-задачами производственного предприятия, возможности решения этих задач современными информационными системами, а также подходы к интеграции этих информационных систем в единый замкнутый контур цифрового производственного предприятия.
Учет производственных факторов
Первой классической задачей производственного планирования является учет производственных факторов. Зачастую инженер по планированию строит производственное расписание, руководствуясь определенными параметрами эффективности: процент просроченных заказов, коэффициент полезной работы оборудования, себестоимость изготовления и т. д. Однако для производства самым важным фактором является выполнимость разработанного расписания. Для обеспечения выполнимости плановику ранее приходилось держать в уме (или, если повезет, в Excel) большой объем информации, начиная от графика планово‑предупредительных работ и заканчивая простудой самого квалифицированного наладчика. Технологии усложнялись и развивались, расширялась номенклатура, добавлялись новые типы оборудования. Факторов, прямо и косвенно влияющих на производственный процесс, становилось все больше и больше: объемы потребления электроэнергии, газа и сжатого воздуха, наличие тары, оснастки, транспорта, персонала, складских площадей и др. Держать все это в голове было совершенно невозможно. Как следствие, появлялись ошибки при планировании, росла план-фактная разница, страдала эффективность и рентабельность производства, а в результате и заказчики продукции.
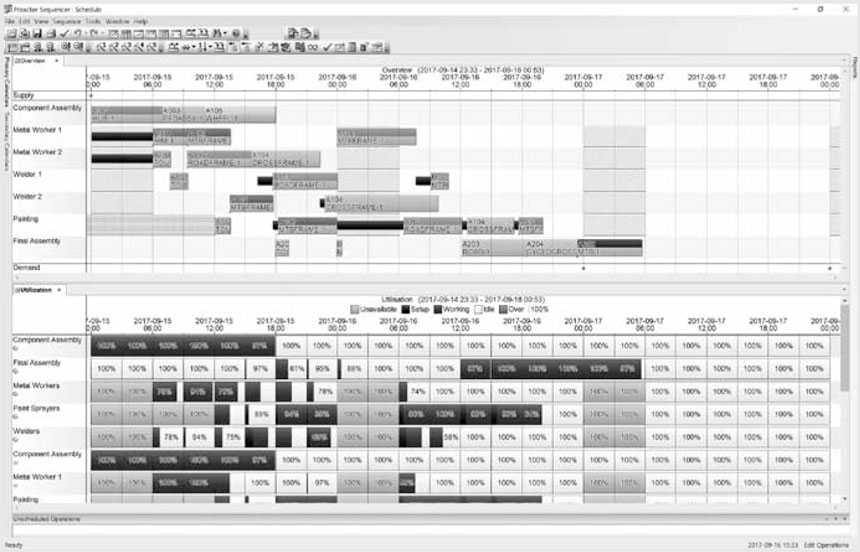
Рис. 2. Пример производственного плана в SIMATIC IT Preactor
Для решения перечисленных задач были разработаны системы класса APS (Advanced Planning & Scheduling). Одной из самых популярных систем такого класса является программный продукт SIMATIC IT Preactor от компании Siemens (рис. 2). С помощью мощных средств интеграции пакет Preactor собирает всю необходимую актуальную информацию из различных производственных источников — систем управления ТОиР, управления персоналом, энергоменеджмента, складского учета и строит производственное расписание. Получаемые алгоритмы и сценарии планирования позволяют плановику оптимизировать расписание по желаемым экономическим параметрам, а о выполнимости заданных требований позаботится Preactor (рис. 3).
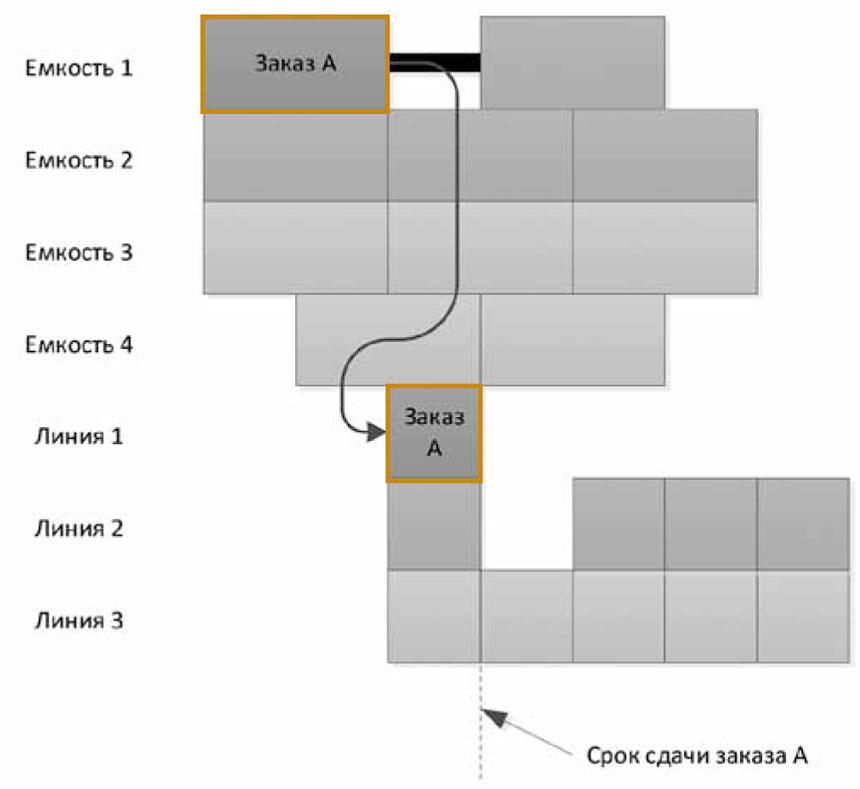
Рис. 3. Оптимизированное расписание в SIMATIC IT Preactor
К сожалению, причины план-фактной разницы далеко не всегда связаны с некорректным планированием. Как бы не шагали вперед технологии, как бы не совершенствовалось оборудование, полностью исключить форс-мажорные ситуации на самом производстве не удается. И, например, при возникновении аварии и последующем ее устранении чаще всего производство возобновляется по той же самой программе, что была в начале смены, а факт выполнения этой программы фиксируется в конце смены. Очевидно, такой подход не выдерживает никакой критики с точки зрения эффективности (рис. 4). Ведь недоступность оборудования из-за аварии — это новые исходные данные, а значит, требуется новый план, оптимизированный и наиболее эффективный в новой реальности. Аналогично, новый план требуется и при возникновении брака из-за некачественной оснастки или сырья, потерях при транспортировке, превышении нормы материала или длительности изготовления. Эти события, меняющие реальность и исходные данные для планирования, возникают хаотично в разных местах производства. И один плановик, даже оснащенный самыми мощными инструментами планирования, не в состоянии «переварить» такой поток информации.
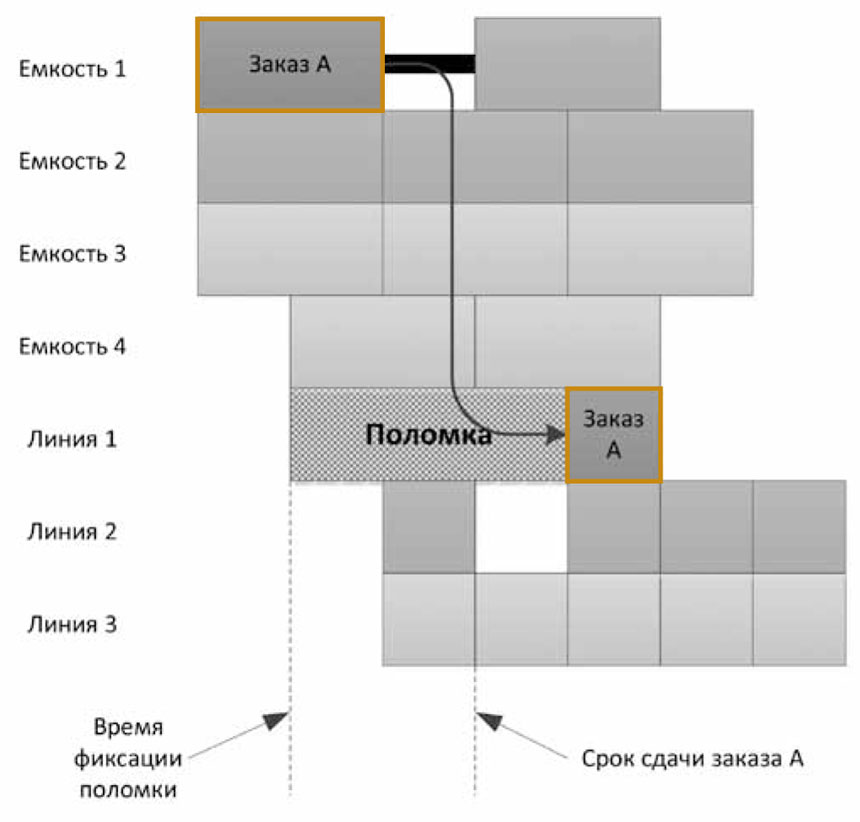
Рис. 4. Просроченный Заказ А из-за поломки линии
Обратная связь от оператора
Отсюда вытекает вторая классическая задача производственного планирования: получение обратной связи от оператора. Ранее эту задачу на производстве было принято решать с помощью промышленных терминалов в рамках систем класса MES. Подобные терминалы позволяют провести аутентификацию оператора, внести фактические данные о начале и окончании операции, потреблении сырья, количестве произведенной продукции и браке, зафиксировать и классифицировать простой оборудования. Однако использование промышленных терминалов на современных производствах имеет ряд значительных недостатков.
Большой объем ручной работы. Первоначально промышленные терминалы использовались исключительно для фиксации факта выполнения операций. Однако с увеличивающимися требованиями к эффективности производства возросли объемы вводимой информации: факт потребления заготовки или сырья, факт потребления инструмента или оснастки, фактические объемы произведенной продукции и брака, плановое время устранения неполадки и др. В результате оператор был вынужден проводить за терминалом много времени, что негативно сказывалось на общей продуктивности.
Низкая скорость доведения информации до «верхнего уровня». Скорость ввода данных в условиях постоянного перепланирования стала критическим фактором. Информация об аварии, введенная через полчаса после инцидента, имеет на порядок меньшую ценность с точки зрения планирования. Ведь за эти полчаса можно было провести наладку на альтернативном оборудовании, перераспределить производственные заказы в соответствии с приоритетом, минимизировать потери. Вместо этого плановик узнает об аварии позже, когда часть оборудования уже занята другими заказами. Еще одной распространенной проблемой использования терминалов является «массовая» фиксация всех производственных фактов оператором в конце смены. В этом случае эффективность использования терминала ничуть не выше обычного закрытия заказ-наряда с помощью бумажного рапорта.
Необходимость присутствия человека. Последняя причина неэффективности промышленных терминалов в условиях всеобщей автоматизации и роботизации очевидна: зачастую на кнопки промышленного терминала просто некому нажимать. В самом деле, не выделять же для этих целей отдельный манипулятор? Все чаще мы слышим о современных «темных» производствах и складах: в них нет не только терминалов, но даже внутреннего освещения. Ведь роботам для работы свет не нужен.
Интеграция с производственным оборудованием
Четвертая промышленная революция, которая подразумевает полную автоматизацию и цифровизацию производства, диктует новые требования к скорости и качеству работы с производственными данными при планировании. И для удовлетворения этих новых требований со стороны бизнеса требуется принципиально новая логика взаимодействия систем. Проблема получения обратной связи от оператора к вспомогательным системам и обеспечивающей производственной инфраструктуре трансформируется в проблему получения обратной связи от оборудования. Для реализации такой логики компанией Siemens были разработаны механизмы интеграции системы планирования SIMATIC IT Preactor и системы сбора данных, управления и диспетчеризации производства на базе платформы SIMATIC WinCC Open Architecture (WinCC OA).
Обширные возможности платформы WinCC OA в области получения информации от оборудования по различным протоколам и интерфейсам, обработки и анализа данных различной природы [2] открывают совершенно новые горизонты для планирования производства.
Например, при возникновении аварии на линии WinCC OA может не только зафиксировать аварийный сигнал на контроллере, но и идентифицировать его, по прямым и косвенным признакам провести оценку вероятного времени возобновления работы и сформировать соответствующее служебное сообщение для SIMATIC IT Preactor. Инструмент PCO (Preactor Communication Object) позволяет запускать скрипт перепланирования автоматически, без участия человека. Таким образом, с момента возникновения аварии до перепланирования, минимизации экономических потерь и выдачи новых заданий в систему управления проходит несколько секунд. При этом модули WinCC OA для мобильных и тонких клиентов позволяют вовремя оповестить всех специалистов и руководителей для организации новой производственной программы, вовремя провести переналадку, изменить подключение линий и конвейеров, последовательность и время выгрузки сырья или заготовок со склада (рис. 5).
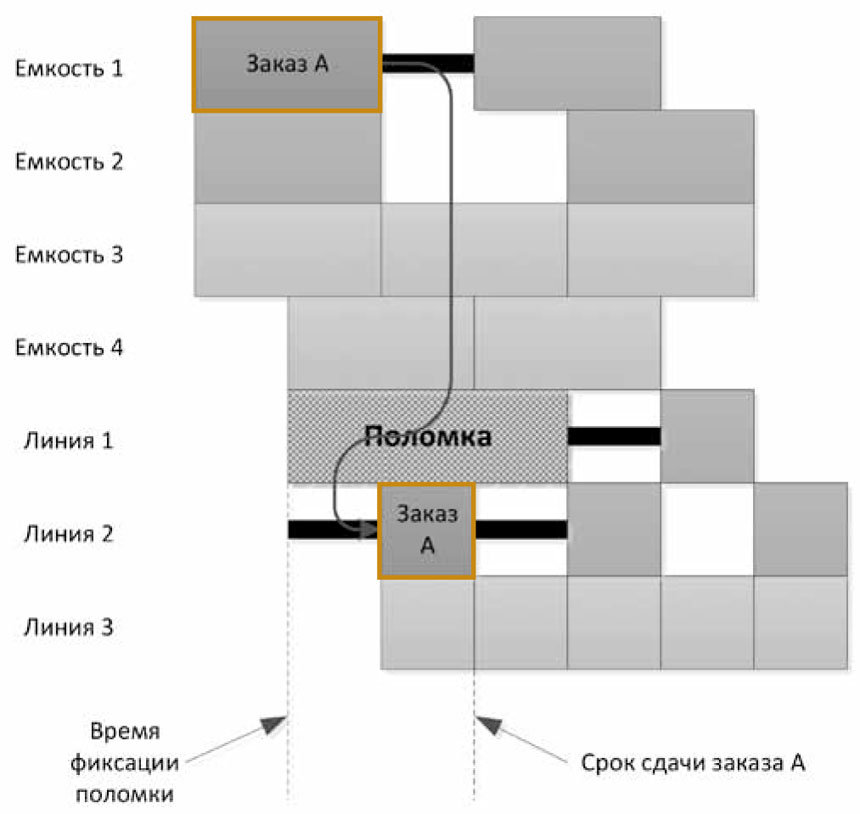
Рис. 5. Перестроенное расписание с помощью связки SIMATIC IT Preactor + WinCC OA
Аналогичным образом можно реализовывать схемы перепланирования при большой разнице запланированного и фактического выпуска, автоматически регистрируя факт с помощью расходомеров или оптических датчиков и автоматически создавая производственные заказы. Еще одним примером такого сценария является автоматическая оценка качества готовой продукции с помощью систем машинного зрения или аппаратных анализаторов и последующее перепланирование, опять же, без участия человека.
А добавив в эту схему систему предиктивной диагностики, можно получить инструмент, способный автоматически осуществлять перепланирование внутри смены в зависимости от конкретных технологических параметров единиц оборудования.
Рассмотренная технология позволяет получить данные непосредственно из оборудования, учесть ранее недоступную, важную информацию и использовать ее для реализации гибких сценариев планирования и перепланирования.
Таким образом, интеграция систем SIMATIC IT Preactor и WinCC OA позволяет построить замкнутый контур производственного планирования от уровня ERP до уровня производственного оборудования (рис. 6) с возможностью гибкого и оперативного перепланирования при изменении внешних или внутренних факторов.
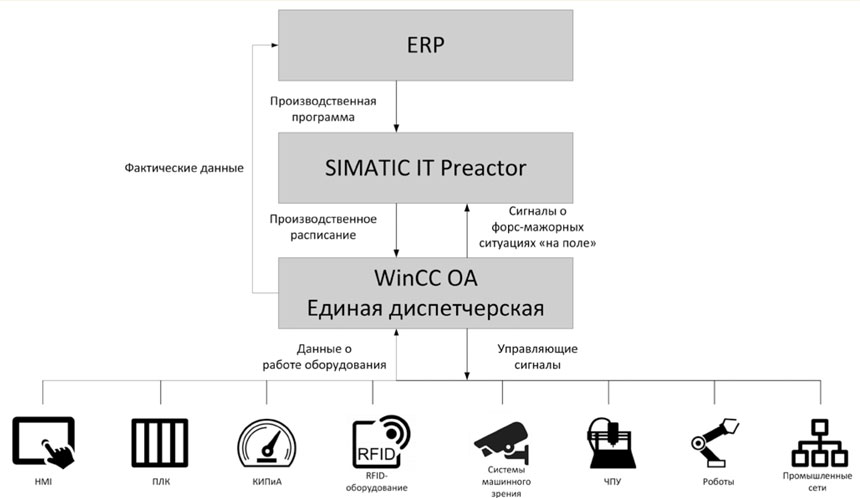
Рис. 6. Интеграция систем SIMATIC IT Preactor и WinCC OA
Выводы
Рассмотренная новая логика взаимодействия информационных систем производственного предприятия — это реальность ближайшего будущего, которая возникла из растущих потребностей со стороны бизнеса. Вчера компьютеры и программы управляли оборудованием, сегодня — всем технологическим процессом, но уже завтра современные технологии будут способны автономно управлять цехами и предприятиями в целом в рамках распределенных цифровых кооперационных цепочек, полностью избавляя персонал от рутинной работы и позволяя сконцентрироваться на инновациях и новых разработках в своей предметной отрасли. Технологии и инструменты для построения таких цифровых производств имеются уже сегодня, и решение задачи гибкого производственного планирования — одна из ключевых составляющих для построения цифровых производственных экосистем будущего, позволяющая сократить дистанцию между производством и потребителями.
1. Флипчарт – магнитно-маркерная доска с креплением для листа или блока бумаги, переворачиваемой по принципу блокнота.
Список литературы:
1. Бекасов Д. Возможности «Сименс» для цифровойтрансформации промышленных производств // Control
Engineering Россия, приложение IIoT. 2018. №5.
2. Соловьёв С.Ю. Дигитализация с SIMATIC WinCC OpenArchitecture: настоящее и будущее // ИСУП. 2017. № 3 (69).
Авторы статьи:
Антонов Илья Александрович – эксперт по цифровизации,
Соловьёв Сергей Юрьевич – канд. техн. наук, руководитель Центра компетенций,
Департамент «Цифровое производство», ООО «Сименс».
Он будет опубликован сразу после проверки модератором. Спасибо, что нашли время, ваше мнение очень важно для нас.